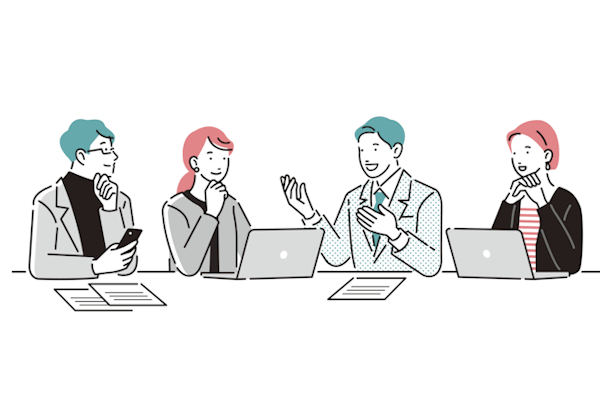
【業界別防水設計アプローチ】自動車、医療機器、ウェアラブルデバイスの特殊要件と対策
電子機器において防水設計は、製品の用途や環境に応じて異なる要件を満たす必要があります。本記事では、自動車、医療機器、ウェアラブルデバイスの3つの業界に焦点を当て、それぞれの特殊要件と防水設計の対策について解説してみたいと思います。
1. 自動車業界における防水設計
自動車業界における特殊要件とは?
- 自動車は雨や洗車時の水、高圧洗浄、水たまりなど、さまざまな水環境にさらされます。
- エンジンルームや車内電子機器は、高温や振動が加わる過酷な条件下で使用されるため、防水性能だけでなく耐熱性や耐振動性も求められます。
- IP規格では、IP67やIP69Kなど、高圧洗浄にも耐える等級が一般的です。
- 防水構造は温度変化による膨張・収縮にも対応を加味し、内圧調整機能などの検討も必要です。
主な設計対策
- シール材の活用:
ゴム製Oリングやガスケットを使用して、水の侵入を防ぎます。 - 防水ベントの採用:
圧力調整を行いながら防水性を確保するため、防水透湿膜付きベントを設置します。 - コネクタ設計:
防水コネクタにはパッキンやインサート成形技術を用い、水漏れを防ぎます。 - 塗装とコーティング:
車体底部にはアンダーコートを施し、防錆効果と防水性能を向上させます。
2. 医療機器業界における防水設計
医療業界における特殊要件とは?
- 医療機器は、清潔さが求められる環境で使用されるため、防水性能だけでなく耐薬品性や洗浄耐性も必要です。
- 手IP規格ではIPX7以上が一般的で、一部機器にはIP68相当の性能が要求されます。
主な設計対策
- シームレス構造:
接合部を最小限に抑えた一体型構造により、水分や汚染物質の侵入リスクを軽減します。 - 耐薬品性材料:
耐腐食性のあるステンレス鋼や特殊プラスチックを筐体材料として使用します。 - 超音波融着技術:
部品間の接合には接着剤ではなく超音波融着を採用し、隙間を完全になくします。 - ポッティング処理:
基板全体を樹脂で封止することで、水分から電子部品を保護します。
3. ウェアラブルデバイス業界における防水設計
ウェアラブルデバイス業界における特殊要件とは?
- ウェアラブルデバイスは日常生活で使用されるため、汗や雨、水泳時の浸水などへの耐性が求められます。
- 軽量性、小型化、美観も重要な要素となります。
- IP規格ではIP67またはIP68が一般的で、一部製品にはATM規格(耐水深度)も適用されます。
主な設計対策
- ナノコーティング技術:
基板や内部部品に薄膜コーティングを施し、防水性能と軽量化を両立します。 - シリコンシール材:
柔軟性が高く、小型デバイスにも適したシール材を採用します。 - 排水機能付き構造:
水分が溜まらないよう、排水孔や疎水加工を施した筐体デザインを採用します。 - ポモジュール化設計:
- 防水性能が必要な部分だけ独立したモジュールとして設計し、全体のコストと重量を抑えます。
まとめ
各業界ごとに異なる環境条件や使用目的に合わせた防水設計が求められます。自動車では耐久性と高圧洗浄への対応、医療機器では清潔さと耐薬品性、ウェアラブルデバイスでは小型化と日常使用への対応が重要です。これらの要件に応じた適切な材料選定と構造設計によって、安全で信頼性の高い製品開発が可能となります。
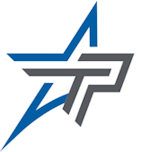
まずはお気軽にお問い合わせください。
製造業も立派なサービス業。
お客様から加工依頼を受けるだけではなく、お客様が抱える問題への本質的な解決につながるヒアリング力とご提案体制でお待ちしております。